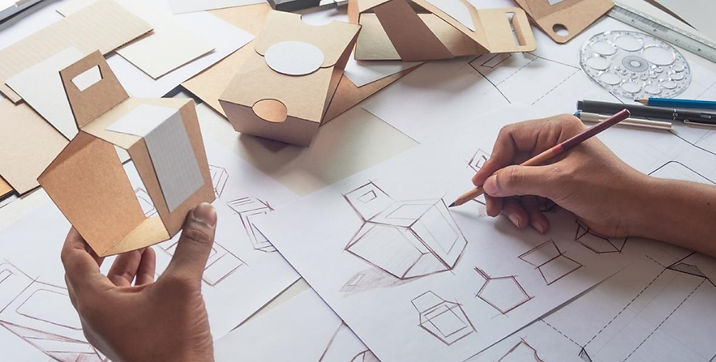


Independently shaping materials using a process
Critical learnings
Establishing the link between manufacturing parameters and material properties
Executing autonomous manufacturing processes
Identifying constraints imposed by the process on the product
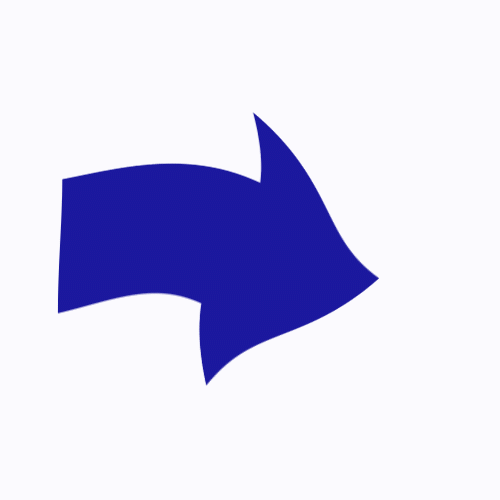
By understanding the impact of the process on properties
By adhering to HSE standards and constraints
By producing a functional product using a specific process
Ce travail m'a permis de comprendre le lien entre matériaux et de mise en forme. Cela consiste à donner une forme déterminée au matériau tout en lui imposant une certaine géométrie, afin d'obtenir un objet ayant les propriétés souhaitées. Dans notre cas : aplanissement + création d'angles droits.
​
Les difficultés rencontrées ont plutôt concerné la communication, je n'avais pas de notion de réalisation et montage vidéo.
​
Ma démarche
-
Réalisation d'un storyboard + script + film de présentation de la dégauchisseuse
-
Recherche sur internet logiciel vidéo --> achat d'un logiciel Movavi vidéo
-
Autoformation en visionnant des tutos insertion images encapsulées + son + musique
-
Création d'un film de présentation de la dégauchisseuse incluant l'aspect HSE

I. Shaping Materials
Case Study: The Jointer
Context :
During a practical activity (SAE) in the first year of the SGM program, I worked in a group of two to study the jointer-planer machine. The objective was to shape materials using this machine while ensuring autonomy and adhering to safety constraints
​
​
​
My Approach
​
​
-
I created a tutorial video explaining how to use the machine while ensuring its safety and the well-being of personnel.
​
-
I wrote a safety sheet to be placed on the machine.
​
-
I trained someone on the use of the jointer.
​
-
I studied the impact of the manufacturing process on the properties of the material.
​​
Reflective analysis
I found this SAE (Student Engineering Activity) interesting because it allowed me to learn how to use a machine independently in the first year, and I was able to train an operator while ensuring safety.
Although I wrote a storyboard, I would have liked to have video editing courses to communicate in a more professional manner. During this project, I realized that the aspect of information transmission is just as important as the technical aspect!
01 - By adhering to HSE standards and constraints
As explained in the competency "Elaborate," HSE (Health, Safety, and Environment) rules are crucial and essential. Therefore, I created a safety data sheet during this SAE, which was posted on the planer machine in the SGM IUT workshop for future operators to reference.

QR-code
02 - By understanding the impact of the process
Impact of the process on the material
The materials, specifically wood in this case, will be flattened during the first pass. During a second pass by changing the orientation of the board, the edge can be flattened, resulting in a right angle.

Forming Process InvestigationII.
Polymer Lab, Individual Work
Context : During the polymer course, the teacher provided a list of products: Perrier-type bottle, plastic bag, cup, felt tip pen cap. The goal was to identify the manufacturing methods through visual inspection and try to find marks or traces of them.
forming process
​
Injection Molding
+
Blow Molding
Why is blow extrusion suitable for thermoplastics? Curious? Click below.
02 - Design and Construction of an Insulated Nest Box
Context : The first instinct to promote bird reproduction is to create substitute habitats. Encouraging controlled colonization, especially through the installation of nest boxes, directly helps combat the decline of certain species.
In this context, in a group of 4, the PSE (Student Engineering Project) "Design and Build a Prototype" was presented to us. The goal was to design and build a nest box that would have the particularity of being thermally insulated. A specific material family, ceramics, was assigned to my project.
Feelings for this project ...
​
Even though the project followed a comprehensive approach: literature review, research on materials and manufacturing processes, thermal simulation, and design using CAD software, it wasn't the SAE that motivated me the most, probably because it lacked the elaboration-characterization aspect and the scientific dimension.
​
Regarding the benefits, it reaffirmed my choice of career path. Moreover, since I was unfamiliar with the material to be used, I took the initiative to meet with potters in the region who provided me with numerous pieces of advice.
The positive aspect is that, thanks to this project, I realized the importance of contacting multiple experts and not settling for a single perspective.
01 - Identifying the constraints imposed by the process on the material
-
I performed visual inspections to identify signs of processing. I found small raised dots, which correspond to the injection points where the material enters the part.
-
I self-trained by watching videos to learn about the processing methods.
-
I understood the close relationship between the shaping process and the material, for example, in this practical work: thermoplastics "melt" reversibly through simple heating (100-200 °C). This property is used for their shaping.
These posters were created during a practical work on polymers, and the skill of implementation was also studied during a specific activity called "nichoir," detailed in the following section.
02 - By understanding the impact of the process on the properties


The product to be made was the birdhouse. I chose natural clay as the material, which dictated the forming process, which was modeling.
Property of clay: hydroplasticity (becomes plastic when water is added), which is a fundamental property with regards to the forming process.
​
Forming process: after molding, the piece has insufficient mechanical strength. It retains some of the water added during shaping. Therefore, it needs to be dried to a green state (formed and dried).
Impact of the process on the properties
​
-
Drying (microwave oven at <50°C) : initially, the clay particles are surrounded by a thin layer of water that separates them from each other. Drying causes a decrease in the spacing between the particles, resulting in shrinkage. Influencing factor on shrinkage: speed of water removal.
​
​
-
Firing (900 - 1400 °C) : its purpose is to increase the density and mechanical strength while reducing porosity. It involves a vitrification reaction (formation of liquid glass that fills a portion of the pore volume).
​
​
-
Cooling : The object becomes dense and resistant. The degree of vitrification determines the properties of the product at room temperature: the higher it is, the more pronounced the strength, durability, and density.

I. Forming materials
Case study: Bulk Molding Compound (BMC)
Context : During a end-of-year SAE (Student Activity Experience) in my first year of the Bachelor's degree, I worked in a group of three to study the parameters influencing the properties of materials.
​
Subject:My topic focused on BMC (Bulk Molding Compound) premix materials, which are a group of semi-finished products resulting from the combination of resins, fillers, and reinforcements in the form of chopped fibers, intended for high-volume molding processes. A typical BMC formulation can consist of 13 different ingredients. The shaping process is done through hot compression under controlled temperature and pressure.
To learn more about the link between manufacturing parameters and material properties,
02 - Respecting the standards

01 - Establishing the link between manufacturing parameters and material properties
Reflective analysis
Through this competency, I realized that often the challenge lies in choosing the most suitable material among the thousands available. This choice involves considering several criteria imposed by the specifications.
Identifying the marks left by manufacturing processes, such as sprues or seams, has made me more observant of the objects around me. Through practical work and projects, I have learned to step back, reflect, and question the results.
​
Gaining more autonomy during SAEs is motivating, even if everything doesn't work on the first attempt. We learn from our mistakes and make progress.
​
Working in a group is smoother, especially for SAEs where everyone's skills (technical or theoretical) complement each other.
​
I also learned, during the SAE Nichoir, to take into account economic factors, which are also of paramount importance in the choice of materials.